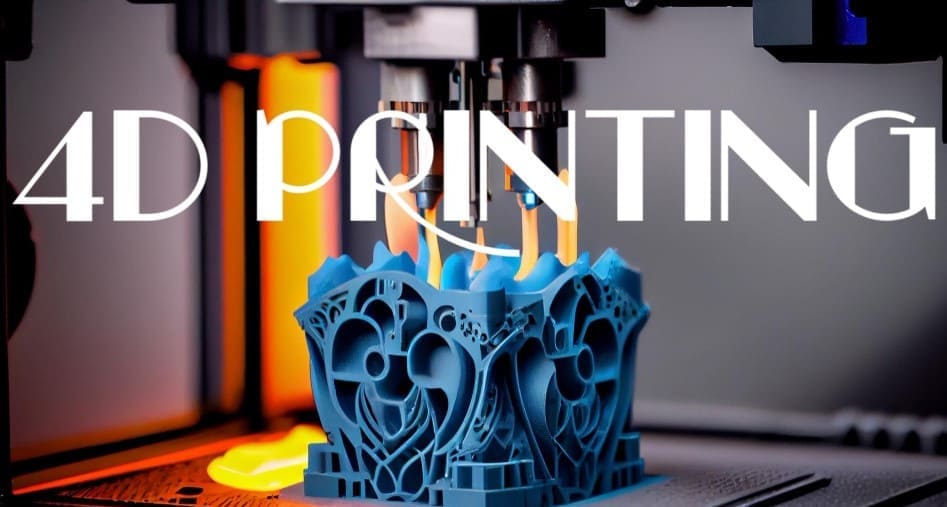
Overview:
To understand what is 4D printing, we need to explore the groundbreaking evolution of additive manufacturing, which extends the capabilities of traditional 3D printing by introducing the dimension of time. Unlike static 3D printed objects, 4D printed items can transform their shape, properties, or functionality in response to environmental stimuli such as temperature, light, or moisture. This dynamic transformation opens up new possibilities for creating innovative products and solutions across a range of industries, from healthcare and construction to consumer goods and aerospace.
As we look to the future, the potential of 4D printing is set to expand dramatically through advancements in smart materials, precision control, and hybrid manufacturing processes. Cutting-edge developments in molecular assembly, AI-driven design, and sustainable production methods promise to enhance the technology’s versatility and impact. By exploring these futuristic advancements, we gain insight into how 4D printing will shape the way we design, produce, and interact with a wide array of products, paving the way for a more adaptable and responsive technological landscape.
Contents:
- What is 4D Printing
- Evolution of 4D Printing
- Key Components of 4D Printing
- How 4D Printing Works
- Key Applications of 4D Printing Across Sectors
- Key Challenges Associated with 4D Printing
- Future Outlook of 4D Printing
- Summing Up
So, what is 4D Printing:
4D printing is an advanced form of 3D printing where the printed objects are designed to change shape, properties, or functionality over time when exposed to external stimuli such as heat, light, moisture, or other environmental factors. The “fourth dimension” refers to the time aspect, meaning the object transforms after its initial creation.
Evolution of 4D Printing:
The evolution of 4D printing is a fascinating journey that builds upon the advancements in 3D printing and material science. Here’s an overview of the key milestones and developments:
1. Early 3D Printing Innovations (1980s-2000s):
1980s: The inception of 3D printing technology, with Charles Hull inventing stereolithography (SLA), laying the foundation for additive manufacturing.
1990s-2000s: Development of various 3D printing techniques like fused deposition modeling (FDM), selective laser sintering (SLS), and digital light processing (DLP), leading to widespread adoption in industries like aerospace, automotive, and healthcare.
2. Introduction of 4D Printing (2013):
2013: Skylar Tibbits, a researcher at MIT, coins the term “4D printing” and introduces the concept in a TED talk. He explains how objects can be printed to change shape over time when exposed to external stimuli, emphasizing the potential for self-assembly and transformation.
3. Advancements in Smart Materials (2013-2015):
2013-2015: Researchers focus on developing smart materials such as shape-memory polymers, hydrogels, and other programmable materials that respond to environmental changes like temperature, humidity, and light. These materials are crucial for 4D printing, enabling dynamic transformations.
4. Integration of Computational Design (2015-2017):
2015-2017: Advances in computational design and simulation tools allow for more precise programming of material behavior. Researchers develop algorithms to predict and control the shape-shifting properties of 4D printed objects, enhancing the accuracy and complexity of transformations.
5. Expansion of Applications (2017-2020):
2017-2020: The potential applications of 4D printing expand significantly. Researchers and industries explore uses in various fields, including:
Medical Devices: Self-adjusting implants, drug delivery systems, and dynamic tissue scaffolds.
Textiles and Fashion: Clothing that adapts to environmental conditions and user preferences.
Construction: Self-assembling structures and responsive building materials.
6. Collaborative Research and Industry Adoption (2020-Present):
2020-Present: Collaborative research efforts between universities, research institutions, and industries accelerate the development of 4D printing. The technology gains traction in sectors like aerospace, automotive, and consumer goods.
Aerospace: Development of lightweight, adaptive components that can change shape for optimized performance.
Automotive: Integration of 4D printed parts for adaptive aerodynamics and interior comfort.
Key Components of 4D Printing:
4D printing relies on several key components that enable it to create objects capable of changing over time in response to external stimuli. Here are the main components:
1. Smart Materials:
Smart materials are at the heart of 4D printing. These materials have the inherent ability to change their properties in response to external stimuli.
Shape-Memory Polymers (SMPs): These polymers can return to a pre-defined shape when exposed to specific stimuli such as heat or light.
Hydrogels: Materials that can swell or shrink in response to water or humidity.
Thermo-responsive Materials: Materials that change their properties with temperature variations.
Photo-responsive Materials: Materials that respond to light exposure.
2. 3D Printing Technology:
Traditional 3D printing technologies are used to fabricate objects with smart materials. The precision and versatility of 3D printing allow for complex geometries and intricate designs.
Fused Deposition Modeling (FDM): A popular 3D printing method that extrudes thermoplastic filaments.
Stereolithography (SLA): Uses a laser to cure liquid resin into hardened plastic in a layer-by-layer fashion.
Selective Laser Sintering (SLS): Uses a laser to fuse powdered material into solid structures.
3. Design and Simulation Software:
Advanced design and simulation software is essential for creating digital models of 4D printed objects and predicting their behavior.
Computer-Aided Design (CAD): Software used to design the 3D model of the object.
Finite Element Analysis (FEA): Simulation tools that predict how materials will respond to external stimuli, ensuring the desired transformation occurs.
Programming Algorithms: Used to encode the specific responses of smart materials into the design.
4. Stimuli:
The external stimuli that trigger the transformation of 4D printed objects are a crucial component. The choice of stimuli depends on the smart material used.
Temperature: Heating or cooling can activate shape-memory polymers.
Moisture: Exposure to water or humidity can trigger hydrogels.
Light: UV or visible light can activate photo-responsive materials.
pH Levels: Changes in pH can cause some materials to expand or contract.
5. Activation Mechanisms:
Activation mechanisms are methods by which the stimuli are applied to the 4D printed object, ensuring the desired transformation.
Heating Elements: Used to apply heat to specific areas of the object.
Water Baths: Submerge the object in water to activate hydrogels.
Light Sources: UV lamps or lasers to trigger photo-responsive materials.
Chemical Solutions: Adjust pH levels to activate pH-responsive materials.
Example: Self-Adjusting Medical Stent
Smart Material: Shape-memory polymer that expands when exposed to body temperature.
3D Printing Technology: SLA printer used to create the intricate structure of the stent.
Design Software: CAD and FEA tools used to design the stent and simulate its expansion behavior.
Stimulus: Body temperature activates the shape-memory polymer.
Activation Mechanism: The stent is inserted in a compact form and expands to fit the artery when exposed to body temperature.
How 4D Printing Works:
4D printing builds on the principles of 3D printing but incorporates smart materials that can change their properties over time in response to external stimuli. Here’s a detailed explanation of how 4D printing works, along with an example to illustrate the concept:
A. The Working Mechanism:
1. Design and Modeling:
The process begins with the design phase, where a digital model of the object is created using CAD software. This model includes the specifications for how the object should transform in response to stimuli.
Computational algorithms are used to predict and control the behavior of the smart materials.
2. Material Selection:
Smart materials, such as shape-memory polymers, hydrogels, or other programmable materials, are chosen based on the desired transformation. These materials have properties that enable them to change shape, stiffness, or other characteristics when exposed to specific environmental conditions.
3. 3D Printing:
The object is printed using traditional 3D printing techniques like fused deposition modeling (FDM), stereolithography (SLA), or selective laser sintering (SLS). The printer deposits layers of the smart material according to the digital model.
During printing, the material is programmed to respond in specific ways to external stimuli. This programming can involve aligning the molecular structure or embedding certain particles within the material.
4. Activation:
Once the printing is complete, the object can be activated by exposing it to the predetermined stimuli. This could be heat, light, moisture, or other environmental factors.
The smart material responds to the stimuli by changing its shape, size, or other properties as programmed.
B. Example: Self-Folding Structure
Step-1. Design:
- A flat sheet is designed using CAD software to fold into a 3D cube when exposed to water. The design includes specific hinge patterns that will fold at certain angles.
Step-2. Material Selection:
- A hydrogel-based smart material is chosen for its ability to expand and contract in response to moisture. The hydrogel is programmed to swell when it absorbs water.
Step-3. 3D Printing:
- The flat sheet is printed using FDM technology. The printer deposits the hydrogel in a precise pattern, creating hinges and folds in the sheet.
Step-4. Activation:
- After printing, the flat sheet is placed in water. The hydrogel absorbs the water and begins to swell at the hinge points.
- As the material swells, the flat sheet starts to fold along the programmed hinge lines, gradually transforming into a 3D cube.
C. Visualization
1. Initial State:
- The object is a flat sheet with specific patterns of smart material printed on it.
2. Exposure to Stimuli:
- When placed in water, the hydrogel material at the hinge points absorbs moisture and expands.
3. Transformation:
- The expansion causes the sheet to fold along the predetermined lines, forming a 3D cube.
4. Final State:
- The flat sheet has fully transformed into a 3D cube, demonstrating the principles of 4D printing.
Key Applications of 4D Printing Across Sectors:
1. Medical and Healthcare:
Self-Adjusting Medical Devices: Implants, stents, and orthopedic devices that can change shape to better fit a patient’s anatomy, enhancing comfort and effectiveness.
Drug Delivery Systems: Capsules that release medication in a controlled manner in response to specific physiological conditions like pH or temperature changes.
Tissue Engineering: Scaffolds that can adapt their properties to support tissue growth and healing, potentially transforming into different structures as needed.
2. Textiles and Fashion:
Adaptive Clothing: Garments that adjust to environmental conditions such as temperature and humidity, providing better comfort and performance for the wearer.
Smart Textiles: Fabrics that can change color or texture in response to external stimuli, offering innovative design possibilities and functional benefits.
3. Construction and Architecture:
Self-Assembling Structures: Components that can change shape and assemble themselves on-site, reducing construction time and labor costs.
Responsive Building Materials: Materials that can adapt to environmental conditions such as temperature or humidity, enhancing energy efficiency and structural performance.
4. Aerospace and Automotive:
Adaptive Components: Parts that can change shape or properties in response to operational conditions, improving aerodynamics, fuel efficiency, and performance.
Self-Healing Materials: Materials that can repair themselves after damage, extending the lifespan of components and reducing maintenance costs.
5. Consumer Goods:
Customizable Products: Items that can change shape or functionality to meet individual user needs, such as furniture that adjusts to different configurations or shoes that adapt to foot shape and activity level.
Responsive Packaging: Packaging that changes shape or properties in response to environmental conditions, providing better protection and longer shelf life for products.
6. Robotics:
Soft Robotics: Robots made from materials that can change shape and stiffness, allowing for more flexible and adaptable movements.
Self-Reconfiguring Robots: Robots that can change their structure to perform different tasks or navigate various environments.
7. Environmental Applications:
Water Management Systems: Components that can adapt to changing water flow or quality, improving the efficiency and effectiveness of water distribution and treatment systems.
Climate-Responsive Structures: Buildings and infrastructure that adjust to changing climate conditions, enhancing resilience and sustainability.
8. Defense and Security:
Adaptive Camouflage: Materials that change color or pattern to blend into different environments, enhancing stealth capabilities.
Deployable Structures: Equipment and shelters that can change shape for easy transport and rapid deployment in the field.
9. Education and Research:
Dynamic Educational Models: Models that change shape or properties to demonstrate scientific principles and phenomena, enhancing learning and engagement.
Responsive Research Tools: Instruments and devices that can adapt to different experimental conditions, improving research capabilities.
Key Challenges Associated with 4D Printing:
1. Material Limitations:
Smart Material Development: The range of smart materials that can be used in 4D printing is currently limited. Developing new materials with reliable and predictable responses to stimuli is essential.
Durability and Stability: Ensuring that smart materials maintain their properties and performance over time, especially under repeated cycles of transformation, can be challenging.
2. Complexity in Design and Modeling:
Design Software: Existing CAD and simulation tools need to evolve to handle the complexity of 4D printed objects, including their dynamic behavior over time.
Predictive Modeling: Accurately predicting how a 4D printed object will behave in response to stimuli requires sophisticated algorithms and significant computational power.
3. Precision and Control:
Printing Accuracy: Achieving the high precision required to ensure that objects transform as intended can be difficult, especially for complex geometries.
Stimulus Control: Precisely controlling the external stimuli (e.g., temperature, moisture, light) to achieve the desired transformation can be challenging, particularly in variable real-world environments.
4. Cost and Scalability:
Production Costs: The cost of smart materials and the advanced 3D printing technology required for 4D printing can be prohibitively high.
Scaling Up: Moving from prototype to mass production involves overcoming significant technical and economic barriers, particularly in industries that require large volumes of products.
5. Regulatory and Safety Concerns:
Medical Applications: For medical devices, extensive testing and regulatory approval are required to ensure safety and efficacy, which can be time-consuming and costly.
Consumer Safety: Ensuring that 4D printed products are safe for consumers, particularly when they change shape or properties, requires thorough testing and adherence to safety standards.
6. Integration with Existing Systems:
Compatibility: Integrating 4D printed components with existing systems and products can be challenging, requiring modifications to design and manufacturing processes.
Standardization: Developing industry standards for 4D printing processes and materials is necessary for widespread adoption.
7. Environmental Impact:
Sustainability of Materials: Developing environmentally friendly smart materials and ensuring that the 4D printing process is sustainable are critical concerns.
Recyclability: Ensuring that 4D printed objects can be recycled or safely disposed of after their useful life is an important environmental consideration.
8. Intellectual Property and Ethical Issues:
IP Protection: Protecting intellectual property in the rapidly evolving field of 4D printing can be challenging, as new materials and methods are developed.
Ethical Considerations: Addressing ethical issues related to the use of 4D printing, particularly in medical and consumer applications, is essential to ensure public trust and acceptance.
Future Outlook of 4D Printing:
1. Ultra-Advanced Smart Materials:
Self-Organizing Materials: Development of materials that can autonomously reconfigure themselves into desired structures without external intervention, leveraging advanced self-assembly principles.
Adaptive Nanomaterials: Creation of materials with nanotechnology that can undergo highly precise and complex transformations at the molecular level, allowing for unprecedented control over material properties and behavior.
2. Breakthroughs in Precision and Control:
Quantum-Scale Printing: Advancements in printing technology to manipulate materials at the quantum scale, enabling the creation of structures with atomic precision and complex functionality.
Programmable Matter: Development of materials that can change their physical properties (e.g., density, elasticity) dynamically and on-demand, using advanced programming techniques embedded during the printing process.
3. Next-Generation Design and Simulation Tools:
Neural Network-Driven Design: Utilization of advanced neural networks and deep learning algorithms to create highly optimized and innovative designs for 4D printed objects, based on extensive simulations and predictive modeling.
Real-Time Adaptive Simulation: Integration of real-time adaptive simulation tools that can adjust predictions and design parameters dynamically as new data is received during the printing process.
4. Revolutionary Manufacturing Processes:
Molecular Assembly: Future 4D printing processes that assemble objects from the molecular level up, allowing for the creation of highly complex and multi-functional structures with precision.
Hybrid Multi-Material Printing: Advanced hybrid printing techniques that combine multiple types of smart materials in a single process, enabling objects with complex, multi-functional, and responsive properties.
5. Next-Level Scalability and Efficiency:
Mass Customization: Development of ultra-fast, scalable 4D printing technologies that enable the mass customization of objects with personalized transformations for a wide range of applications.
Energy-Optimized Processes: Innovative methods to reduce the energy consumption of 4D printing, including the use of energy-harvesting materials and efficient activation mechanisms.
6. Advanced Integration with Emerging Technologies:
Biological Integration: Integration of 4D printing with synthetic biology to create living, biohybrid materials that can grow, heal, and adapt in real-time, merging biological and synthetic systems.
AI-Enhanced Automation: Use of advanced AI and machine learning to automate and optimize the entire 4D printing process, including real-time decision-making for material behavior and transformation.
7. Sustainability and Environmental Innovations:
Eco-Friendly Smart Materials: Development of fully biodegradable or recyclable smart materials that maintain high performance while minimizing environmental impact.
Climate-Responsive Infrastructure: Creation of 4D printed components that can actively respond to and mitigate the effects of climate change, such as buildings that adjust their insulation properties in response to weather conditions.
8. Regulatory and Ethical Advancements:
Global Standards: Establishment of comprehensive global standards and frameworks for 4D printing to ensure safety, interoperability, and ethical considerations across industries.
Ethical AI Integration: Development of ethical guidelines and frameworks for integrating AI with 4D printing, addressing issues related to privacy, security, and the responsible use of advanced technologies.
Summing Up:
The future of 4D printing is poised to revolutionize various industries through advancements in smart materials and manufacturing technologies. Innovations such as self-organizing and adaptive nanomaterials, coupled with breakthroughs in quantum-scale printing and programmable matter, will enable the creation of highly complex and responsive structures. Enhanced design tools driven by neural networks and real-time simulations will further refine the precision and functionality of 4D printed objects, while hybrid manufacturing processes and scalable technologies will facilitate mass customization and efficient production.
Additionally, the integration of 4D printing with emerging technologies like synthetic biology and AI will lead to the development of biohybrid materials and automated, intelligent printing systems. As sustainability becomes a key focus, eco-friendly materials and climate-responsive infrastructure will address environmental challenges. With the establishment of global standards and ethical frameworks, 4D printing will advance towards widespread adoption, delivering innovative solutions and shaping a more adaptable and sustainable future.
Courtesy Image: FreePik