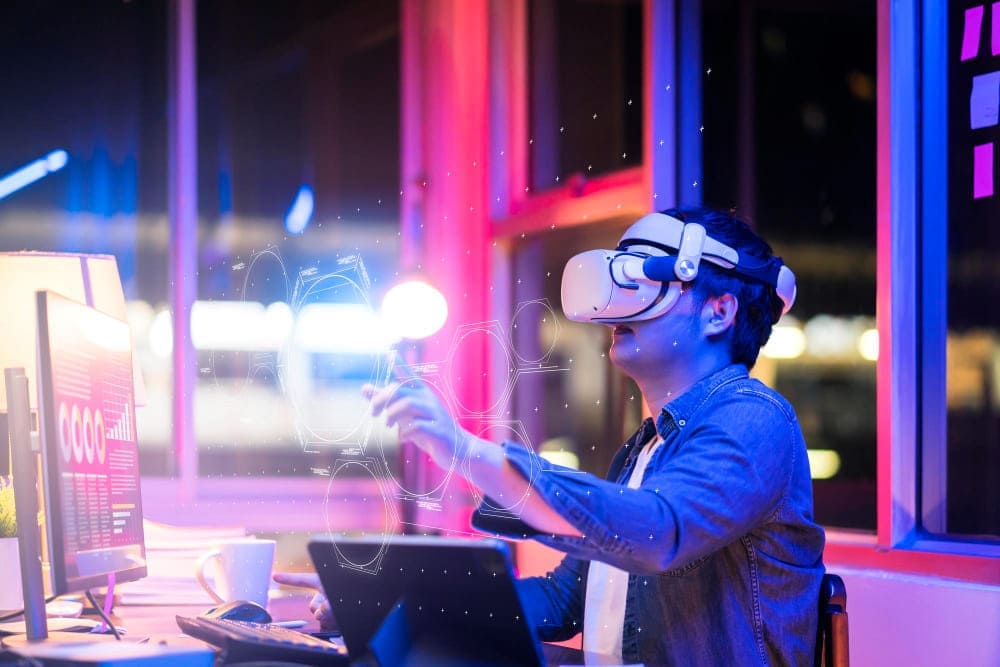
Overview:
In the era of digital transformation, the industrial metaverse emerges as a groundbreaking concept, redefining how industries operate and innovate. By seamlessly blending advanced technologies such as virtual reality (VR), augmented reality (AR), artificial intelligence (AI), digital twins, and the Internet of Things (IoT), the industrial metaverse creates immersive and interconnected virtual environments tailored specifically for industrial applications. Gone are the days of traditional industrial practices; instead, companies are embracing this digital ecosystem to optimize processes, predict maintenance needs, and enhance safety through immersive training and real-time remote assistance.
The industrial metaverse offers a myriad of benefits that revolutionize industrial operations across various sectors. From increased efficiency and reduced downtime to improved safety and sustainability, its impact is profound and far-reaching. By leveraging digital twins for simulation, AI for predictive analytics, and AR/VR for immersive experiences, companies can achieve unparalleled levels of productivity, innovation, and resilience. However, realizing the full potential of the industrial metaverse requires overcoming significant challenges, including high initial investment costs, data security concerns, integration complexities, skill gaps, and regulatory compliance issues. As industries navigate these challenges and embrace emerging trends, the future of the industrial metaverse holds immense promise, paving the way for a new era of industrial excellence and transformation.
Contents:
- What is Industrial Metaverse
- The Key Components of Industrial Metaverse
- The Key Application Areas of Industrial Metaverse
- The Key Benefits of Industrial Metaverse
- The Key Challenges in Industrial Metaverse
- The Future of Industrial Metaverse
- Summing Up
So, What is the Industrial Metaverse:
The industrial metaverse is a digital ecosystem that blends advanced technologies like virtual reality (VR), augmented reality (AR), artificial intelligence (AI), digital twins, and the Internet of Things (IoT) to create immersive and interconnected virtual environments specifically for industrial applications. This concept extends the traditional metaverse, which is often associated with social and entertainment purposes, to industrial sectors such as manufacturing, construction, and logistics.
What are the Key Components of Industrial Metaverse:
1. Digital Twins:
Digital twins are virtual replicas of physical assets, systems, or processes. In the industrial metaverse, they are used to simulate, monitor, and optimize real-world operations.
2. Virtual and Augmented Reality:
VR and AR technologies provide immersive experiences for training, remote assistance, and design visualization. AR, in particular, overlays digital information onto the physical world, aiding in maintenance and assembly tasks.
3. Artificial Intelligence and Machine Learning:
AI and ML algorithms analyze data from connected devices and sensors to optimize processes, predict failures, and improve decision-making.
4. Internet of Things (IoT):
IoT devices collect and transmit data from physical assets, enabling real-time monitoring and control within the industrial metaverse.
5. Blockchain:
Blockchain technology ensures data security, transparency, and immutability, which is crucial for maintaining trust in digital transactions and records within the industrial metaverse.
Now Let’s Understand the Key Applications of Industrial Metaverse:
1. Predictive Maintenance:
By using sensors, IoT devices, and AI algorithms, companies can predict equipment failures before they occur.
Example:
Siemens uses digital twins and AI to monitor machinery in real-time. By analyzing data patterns, Siemens can predict when a machine part is likely to fail, allowing maintenance to be performed proactively, reducing downtime and maintenance costs.
2. Remote Monitoring and Assistance:
AR and IoT enable real-time remote monitoring and troubleshooting, allowing experts to assist on-site workers from anywhere in the world.
Example:
Honeywell utilizes AR glasses for remote assistance. Field technicians wear AR glasses that stream live video to remote experts who can guide them through complex procedures, overlaying instructions and diagrams onto their field of view. This reduces the need for travel and accelerates problem resolution.
3. Training and Simulation:
VR environments provide immersive training experiences for workers, allowing them to practice skills in a risk-free, virtual setting.
Example:
Walmart employs VR training modules for employee training. Workers can simulate handling emergency situations, customer interactions, and equipment operations. This type of training improves preparedness and reduces on-the-job errors.
4. Product Design and Testing:
Engineers can create digital prototypes and test them in virtual environments, iterating quickly and cost-effectively.
Example:
Ford uses VR to design and test vehicle models. Designers and engineers can immerse themselves in virtual car interiors and exteriors to assess aesthetics, ergonomics, and functionality. This speeds up the design process and reduces the need for physical prototypes.
5. Supply Chain Optimization:
Integrating data from various sources provides a comprehensive view of the supply chain, optimizing logistics, inventory management, and production planning.
Example:
DHL leverages AR and digital twins for warehouse management. Workers use AR glasses that display optimal picking routes and real-time inventory information, streamlining the picking process and reducing errors. Digital twins model the entire supply chain to identify bottlenecks and optimize logistics.
6. Enhanced Collaboration:
Virtual environments facilitate real-time collaboration between teams across different locations, enabling them to work together on complex projects.
Example:
Dassault Systemes offers the 3DEXPERIENCE platform, which allows global teams to collaborate on product design and development. Teams can work together in a shared virtual space, reviewing designs, making adjustments, and conducting virtual walkthroughs, enhancing collaboration and reducing development times.
7. Smart Manufacturing:
Integrating IoT, AI, and digital twins to create highly automated and efficient manufacturing processes.
Example:
General Electric (GE) employs digital twins and AI in their manufacturing plants. By modeling the entire production line digitally, GE can optimize operations, predict maintenance needs, and adapt to changes in demand quickly, leading to more efficient and flexible manufacturing processes.
8. Quality Control:
Using AI and digital twins to monitor and ensure product quality throughout the manufacturing process.
Example:
BMW uses AI-powered cameras and sensors to inspect parts during assembly. The data is compared against digital twins to identify defects and deviations in real-time, ensuring high-quality standards and reducing waste.
9. Construction and Infrastructure:
Virtual modeling and simulation for planning and managing construction projects.
Example:
Bentley Systems provides software for creating digital twins of infrastructure projects. Construction firms can simulate and visualize entire projects before breaking ground, optimizing design, planning logistics, and anticipating potential issues, leading to more efficient and successful project execution.
10. Energy Management:
Using digital twins and IoT for monitoring and optimizing energy consumption in industrial facilities.
Example:
Schneider Electric utilizes digital twins to manage energy usage in their facilities. By monitoring real-time data from various systems, they can optimize energy consumption, reduce costs, and minimize environmental impact.
Now, Let’s Explore the Key Benefits of Industrial Metaverse:
1. Increased Efficiency:
Optimized Processes: Digital twins and AI enable real-time monitoring and analysis of industrial processes, allowing for continuous optimization and reducing inefficiencies.
Example: In manufacturing, digital twins can simulate production lines to identify and rectify bottlenecks, leading to smoother operations and higher output.
2. Reduced Downtime:
Predictive Maintenance: AI and IoT can predict equipment failures before they occur, allowing for proactive maintenance and reducing unplanned downtime.
Example: Companies like Siemens use predictive maintenance to schedule repairs during planned downtime, avoiding costly interruptions in production.
3. Enhanced Safety:
Virtual Training: VR provides a safe environment for training workers on hazardous tasks, reducing the risk of accidents.
Remote Assistance: AR allows experts to guide on-site workers through complex procedures remotely, minimizing the need for risky on-site interventions.
Example: Oil and gas companies use VR for emergency response training, ensuring that employees are well-prepared for real-life scenarios.
4. Improved Quality:
Real-Time Quality Control: AI and digital twins enable continuous monitoring of production quality, ensuring that defects are detected and addressed promptly.
Example: BMW’s AI-powered inspection systems catch defects early in the assembly process, ensuring high-quality standards are maintained.
5. Cost Savings:
Efficient Resource Use: Optimizing processes and reducing waste leads to significant cost savings in materials, energy, and labor.
Reduced Travel: Remote monitoring and assistance reduce the need for travel, saving time and expenses.
Example: Logistics companies use digital twins to optimize routing and inventory management, reducing fuel consumption and operational costs.
6. Accelerated Innovation:
Rapid Prototyping: Digital twins and VR allow for quick iteration and testing of designs, speeding up the development cycle.
Collaborative Design: Virtual environments facilitate collaboration across teams and locations, fostering innovation and creativity.
Example: Automotive companies like Ford use VR to rapidly prototype and test new vehicle designs, accelerating the innovation process.
7. Sustainability:
Energy Efficiency: Monitoring and optimizing energy consumption in real-time leads to more sustainable operations.
Reduced Waste: Improved process efficiency and quality control minimize material waste.
Example: Schneider Electric uses digital twins to manage energy consumption in their facilities, reducing their carbon footprint.
8. Enhanced Collaboration:
Virtual Workspaces: Teams can work together in shared virtual environments, regardless of their physical location, enhancing communication and collaboration.
Example: Dassault Systèmes’ 3DEXPERIENCE platform allows global teams to collaborate on product design and development, improving coordination and innovation.
9. Better Decision-Making:
Data-Driven Insights: AI and machine learning analyze vast amounts of data to provide actionable insights, aiding in informed decision-making.
Scenario Simulation: Digital twins allow companies to simulate different scenarios and assess their potential impacts before making decisions.
Example: GE uses digital twins to model different production scenarios, enabling better planning and resource allocation.
10. Scalability and Flexibility:
Adaptable Operations: The industrial metaverse allows companies to quickly adapt to changing market demands and operational requirements.
Scalable Solutions: Virtual environments and digital twins can be scaled to accommodate growing operations or new projects.
Example: Manufacturing plants can quickly reconfigure production lines virtually to meet new product demands without extensive downtime.
While the Industrial Metaverse Offers Numerous Benefits, It Also Presents Several Challenges:
1. High Initial Investment:
Infrastructure Costs: Implementing the industrial metaverse requires significant investment in hardware, software, and network infrastructure.
Example: Companies need to invest in IoT devices, high-speed networks, VR/AR equipment, and advanced computing systems, which can be cost-prohibitive, especially for small and medium-sized enterprises (SMEs).
2. Data Security and Privacy:
Cybersecurity Threats: The integration of IoT devices and interconnected systems increases vulnerability to cyberattacks.
Data Privacy: Ensuring the privacy of sensitive industrial data is crucial, especially when using cloud-based solutions.
Example: Manufacturing plants collecting extensive data on production processes must safeguard against data breaches that could result in intellectual property theft or operational disruptions.
3. Integration with Legacy Systems:
Compatibility Issues: Many industrial operations still rely on legacy systems that may not be easily integrated with new digital technologies.
Complex Upgrades: Upgrading or replacing legacy systems can be complex, time-consuming, and costly.
Example: An older manufacturing plant with outdated control systems may face challenges integrating new IoT sensors and digital twins.
4. Technical Expertise:
Skill Gaps: Implementing and managing the industrial metaverse requires specialized skills in areas like AI, VR/AR, IoT, and cybersecurity.
Training Needs: Existing staff may need extensive training to adapt to new technologies and workflows.
Example: Companies may struggle to find qualified personnel who can develop and maintain digital twins or manage AI-driven predictive maintenance systems.
5. Scalability Issues:
Resource Constraints: Scaling digital solutions across large industrial operations can be resource-intensive and challenging.
Infrastructure Limitations: Ensuring that the underlying infrastructure can handle increased data loads and connectivity requirements is essential for scalability.
Example: A global logistics company may find it challenging to implement a consistent and scalable digital twin solution across all its warehouses.
6. Regulatory Compliance:
Industry Regulations: Different industries have specific regulations that must be adhered to when implementing new technologies.
Data Regulations: Compliance with data protection laws, such as GDPR, adds complexity to managing data within the industrial metaverse.
Example: Pharmaceutical companies must ensure that their digital processes comply with strict regulatory standards for data integrity and traceability.
7. Interoperability:
Standardization: The lack of standardized protocols and platforms can hinder interoperability between different systems and devices.
Vendor Lock-In: Companies may become dependent on specific vendors, limiting their flexibility and options.
Example: A factory using IoT devices from different manufacturers may face difficulties in integrating these devices into a unified digital twin platform.
8. Data Management and Quality:
Data Overload: The vast amount of data generated by IoT devices and digital twins can be overwhelming to manage and analyze.
Data Accuracy: Ensuring the accuracy and reliability of data is crucial for effective decision-making and process optimization.
Example: Inaccurate sensor data in a digital twin model could lead to incorrect predictions and suboptimal maintenance scheduling.
9. Change Management:
Resistance to Change: Employees may resist adopting new technologies and workflows, especially if they are not well-understood or if there are concerns about job displacement.
Cultural Shifts: Successfully implementing the industrial metaverse requires a cultural shift within organizations to embrace digital transformation.
Example: Workers in a traditional manufacturing plant may be hesitant to adopt VR-based training programs or AI-driven decision-making tools.
10. Environmental Impact:
Energy Consumption: The computing power required for AI, VR/AR, and other digital technologies can lead to increased energy consumption and associated environmental impacts.
Sustainable Practices: Ensuring that the implementation of the industrial metaverse aligns with sustainability goals can be challenging.
Example: Data centers supporting industrial metaverse applications need to adopt energy-efficient practices to mitigate their environmental footprint.
So, What is the Future of Industrial Metaverse:
1. Advanced Digital Twins:
Integration with AI and Machine Learning: Digital twins will become more intelligent, using AI and machine learning to provide deeper insights, predictive analytics, and autonomous decision-making.
Enhanced Realism and Detail: Improvements in simulation technology will enable digital twins to replicate physical processes and environments with greater accuracy and detail.
Example: Future digital twins in the automotive industry could simulate entire production lines, predicting and optimizing every aspect from material flow to worker ergonomics.
2. Widespread Adoption of AR and VR:
Improved Hardware: Advances in AR and VR hardware will make these technologies more accessible, comfortable, and user-friendly, leading to broader adoption in industrial settings.
Immersive Training and Remote Work: AR and VR will become standard tools for training, remote assistance, and collaborative work, breaking down geographical barriers.
Example: Construction workers using AR glasses for real-time overlays of building plans and VR for immersive safety training scenarios.
3. IoT and Edge Computing Integration:
Real-Time Data Processing: Edge computing will enable real-time data processing and analytics at the source, reducing latency and improving response times.
Enhanced Connectivity: The proliferation of 5G and beyond will support the massive data exchange required for real-time industrial applications, enhancing connectivity and efficiency.
Example: Smart factories utilizing edge computing to analyze data from hundreds of IoT sensors in real-time, optimizing production processes on the fly.
4. AI-Driven Automation and Decision-Making:
Autonomous Operations: AI will drive the automation of more complex industrial processes, enabling autonomous operations and reducing human intervention.
Predictive and Prescriptive Analytics: AI will not only predict issues but also prescribe optimal solutions, further enhancing decision-making capabilities.
Example: AI systems in energy plants autonomously managing energy distribution based on real-time demand and supply data.
5. Enhanced Cybersecurity Measures:
AI-Powered Security: AI and machine learning will be used to enhance cybersecurity, detecting and responding to threats in real-time.
Blockchain for Data Integrity: Blockchain technology will ensure data integrity and security, providing transparent and tamper-proof records of all transactions and processes.
Example: Industrial networks employing AI to monitor anomalies and blockchain to secure data from IoT devices.
6. Sustainable and Green Technologies:
Energy-Efficient Solutions: The industrial metaverse will adopt more energy-efficient technologies and practices, aligning with global sustainability goals.
Circular Economy Integration: Digital twins and AI will help optimize resource use and promote circular economy practices, reducing waste and environmental impact.
Example: Manufacturing plants using digital twins to design products that are easier to recycle and reuse, reducing their overall environmental footprint.
7. Greater Interoperability and Standardization:
Unified Platforms: Industry-wide standards and protocols will emerge, ensuring interoperability between different systems and devices.
Collaborative Ecosystems: Companies will create more collaborative ecosystems, sharing data and insights across platforms to enhance overall efficiency and innovation.
Example: A consortium of manufacturers developing shared standards for digital twin data formats, enabling seamless collaboration and data exchange.
8. Human-Centric Design and User Experience:
Intuitive Interfaces: Future industrial metaverse applications will feature more intuitive and user-friendly interfaces, making it easier for workers to interact with complex systems.
Augmented Workforce: AR and VR will augment the capabilities of the workforce, providing real-time assistance, reducing errors, and improving productivity.
Example: Maintenance technicians using AR interfaces that guide them step-by-step through complex repairs, enhancing accuracy and reducing training time.
9. Enhanced Collaboration and Remote Work:
Global Teams: Virtual environments will enable global teams to collaborate seamlessly, breaking down physical barriers and fostering innovation.
Virtual Workspaces: Companies will increasingly adopt virtual workspaces for meetings, design reviews, and project management, enhancing remote work capabilities.
Example: Engineering teams from different continents collaborating in a shared virtual workspace to design and test new products in real-time.
10. Evolving Business Models:
As-a-Service Models: More companies will offer industrial metaverse technologies as services, making advanced capabilities accessible without large upfront investments.
Innovation Hubs: Organizations will establish innovation hubs and labs dedicated to exploring and developing new applications of the industrial metaverse.
Example: A company offering digital twin technology as a service, enabling manufacturers to optimize their operations without investing in the underlying infrastructure.
Summing Up:
The industrial metaverse integrates advanced technologies like VR, AR, AI, digital twins, and IoT to create interconnected virtual environments for industrial applications. This digital ecosystem enhances industrial operations by optimizing processes, predicting maintenance needs, improving safety through immersive training, and enabling real-time remote assistance. The key benefits include increased efficiency, reduced downtime, enhanced safety, improved quality, cost savings, accelerated innovation, sustainability, enhanced collaboration, better decision-making, and scalability. These advantages collectively lead to more effective and resilient industrial operations, driving significant improvements across various sectors.
However, implementing the industrial metaverse comes with challenges such as high initial investment costs, data security and privacy concerns, integration with legacy systems, skill gaps, scalability issues, regulatory compliance, interoperability, data management and quality, resistance to change, and environmental impact. The future of the industrial metaverse looks promising, with expected advancements in intelligent digital twins, widespread adoption of AR/VR, integration of IoT and edge computing, AI-driven automation, enhanced cybersecurity, sustainable technologies, greater interoperability, human-centric design, enhanced collaboration, and evolving business models. These trends will further transform industrial operations, offering significant opportunities for growth and innovation while requiring strategic planning and adaptation to overcome existing challenges.